Project Information
Name:
Interchange 55
Logistics Park
Romeoville, IL
Product: AB Classic
Size: 32,000 ft2 (3,000 m2)
Wall Builder:
Classic Landscape
West Chicago, IL
Engineer:
Virgilio & Assoc.
Lake Zurich, IL
Allan Block Manufacturer:
Reading Rock
Cincinnati, OH
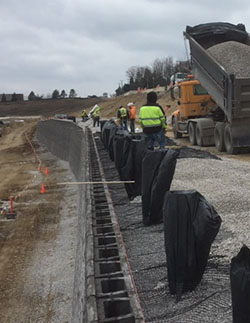
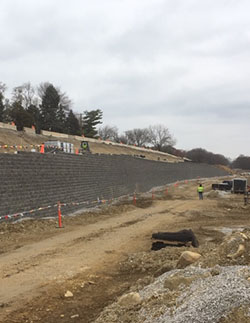
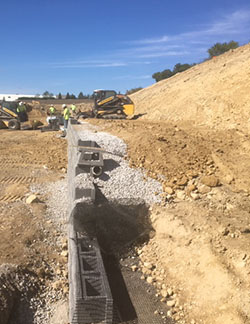
Combining Geogrid Reinforcement and Soil Nails on Project was Best Option
When CT Realty decided to develop a roughly 120-acre site in Romeoville, Illinois for a new Industrial Park, they had many site considerations. With most of the flat development sites in the area used up, CT Realty worked with Jacob & Hefner Associates to fit two 650,000 ft2 (60,000 m2) buildings on the site with over 100 ft of grade change across the property. As you can imagine, multiple retaining walls were required to provide the necessary parking and building area for the site.
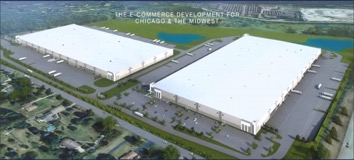
Plan:
CT Realty hired Clayco in order to streamline the process for the complex design-build site. Clayco began putting together a team that could tackle all portions of this massive site and complete the process the most efficiently. Virgilio & Associates was brought into the project to begin looking at the various retaining walls that would be needed on site. Ryan Freund, one of Virgilio & Associates design engineers, started by narrowing down the type of walls to be placed on site. During Freund’s review of the site, he explored options with sheet piles, cast in place, big block, and finally ended on a segmental retaining wall (SRW). He found that an SRW design would give him the most flexibility on the site which was going to require multiple reinforcement options to make the project a success.
Design:
Once a general plan was developed, Reading Rock (licensed Allan Block manufacturer) began working with the design team to see what type of reinforcement options would best fit the site. Throughout the process, Freund looked at reinforcement options for use with the SRW such as geogrid reinforcement, No-Fines concrete, soil nails, and sheet piles. A geogrid application typically provides the most cost-effective solution and that was the first choice of the design team and owner. The Allan Block engineering department was consulted to review various options and while reviewing the site with Virgilio & Associates, global stability was quickly found as the controlling factor. As stated by Ryan Freund of Virgilio & Associates, the location of the retaining wall system quickly became a major design problem. Bill Wyzgala with Midland Standard Engineering & Testing was brought into the design team to review the reinforcement options and establish a working global stability model, in order to maximize the space on site. By evaluating the site stability, it was determined that most walls could use geogrid reinforcement, but two of the retaining walls would encroach on adjacent properties which had to be addressed with a solution other than geogrid. Clayco and the rest of the design team reviewed three final options for those two walls which included; sheet piles, soil nails, or work out a deal with the neighboring property owners. Thankfully, a successful negotiation led to the receipt of a construction/temporary easement. However, one property would not allow encroachment due to a new roadway that had just been placed. The next option was to review sheet piles and soil nails for that wall. Due to cost and aesthetics involved with sheet piles, soil nails were selected as the reinforcing option while facing the wall with the same SRW block as the rest of the site.
Build:
Classic Landscape, an Allan Block Master Wall Builder, secured the project and was ready to tackle the installation of all walls on site, including the soil nail wall. Classic Landscape worked diligently with Reading Rock and the design team to come up with a solution to the site while using a product line that is economical and very efficient to install. Coincidentally, the AB Classic block was selected for just those reasons and installation was ready to begin.
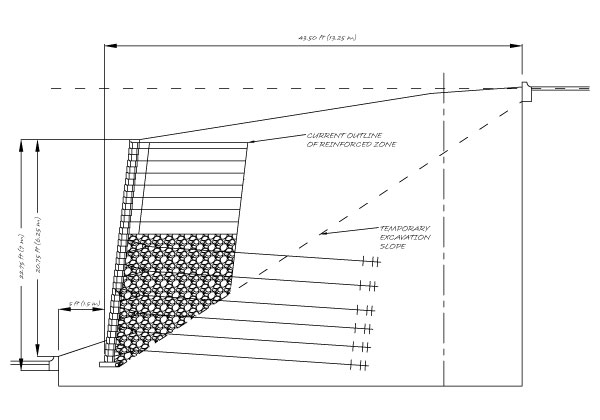
Since the project had to be fast tracked in a design-build approach, Classic Landscape began installing the geogrid reinforced retaining walls while Virgilio & Associates ran their design on the soil nail wall. Freund used the common spreader bar application at the excavated cut to allow geogrid to be placed between the Allan Block units, wrap around the spreader bar, and return to the block facing 2 courses higher. Although soil nails were designed for the full height, Clayco’s Design team looked at the site excavation and the location of the soil nails in 3D to find out where Classic Landscape could transition to geogrid reinforcement to keep the wall as economical as possible for CT Realty. Classic Landscape had to pay special attention to these unique details all while coordinating with the installation of the soil nails to ensure a seamless process.
Ryan Freund commented that Clayco did a great job in coordinating this site between so many parties on both the design and construction side. The teamwork done by the design group led to a successful project in Romeoville.