Project Information
Name:
Vintage at SLO Apartment Homes
San Luis Obispo, CA
Product: AB Classic
Size: 8,800 ft2 (818 m2)
Wall Builder:
Homeland Engineering
Wall Designer:
Smith Structural Group
and AB Engineering
Allan Block Manufacturer:
Air Vol Block
San Luis Obispo, CA
Allan Block: The Solution to Problematic Site Conditions
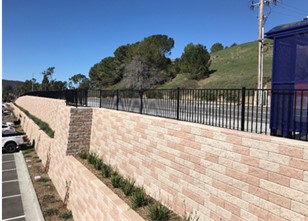
Vintage at SLO Apartment Homes is a luxury apartment complex located just two miles southeast of downtown San Luis Obispo, CA; offering its residents luxury living without sacrificing convenience. The community consists of seven apartment buildings with 105 individual units. When the developer, Abbott Reed Inc., was designing this community, they realized they needed a solution to create the required parking for its residents. The problem with creating parking for this complex was the adjacent roads averaged an elevation of 15 ft (4.5 m) above the proposed apartment complex elevation. The road was also being widened to accommodate increased traffic loads and they needed to add space for a bus stop. The developers originally looked at a cast-in-place retaining wall to create usable land but when faced with exorbitant costs, they turned to Allan Block for a better solution.
Plan:
This area is geologically difficult to build on due to the poor clay soils and high seismic risk, so the developers originally thought a cast-in-place wall would be the best solution. They reached out to Smith Structural Group to design a masonry cast-in-place wall. They received the design back and found that the cast-in-place wall would require a massively oversized footing. Faced with excessive costs, the developers reached out to Erik Geil, an Allan Block specialist and sales representative for Air Vol Block, for possible solutions.
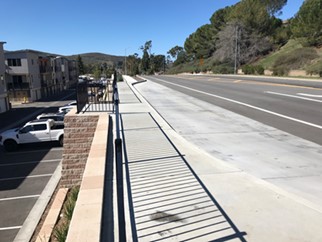
When Erik met with Abbott Reed Inc., he saw the opportunity to save them a lot of money by going with an Allan Block product. The developers did not think a segmental retaining wall would even be an option on this project because the reinforcement would encroach the property lines. To maximize the parking space available, the developers needed the retaining wall to be as close to the road as possible, within 6 ft (1.8 m) at some locations. With traditional forms of reinforcement like geogrid, a 15 ft (4.5 m) tall wall in good soil conditions would require a minimum of 9 ft (2.7 m) of geogrid. While the developers could have chosen to bury the geogrid below the road, they were worried about future utility maintenance causing damage to the geogrid. Erik mentioned that No-Fines Concrete would be a great alternative to a traditional geogrid segmental retaining wall.
No-Fines Concrete (NFC) is comprised of a coarse aggregate material in a 6 to 1 ratio with cement. The absence of fine particles creates voids in the concrete allowing for water to drain through the system. When using Allan Block products with NFC, the permeable concrete actually attaches to the back of the block and extends the depth of the retaining wall mass. Typical geogrid reinforced retaining walls require an excavation depth of 60% or more of the wall height; while a NFC backfill retaining wall with similar site conditions, requires only 30 to 40% of the wall height. Limiting the excavation depth helps the contractors install the wall quicker, thus saving money.
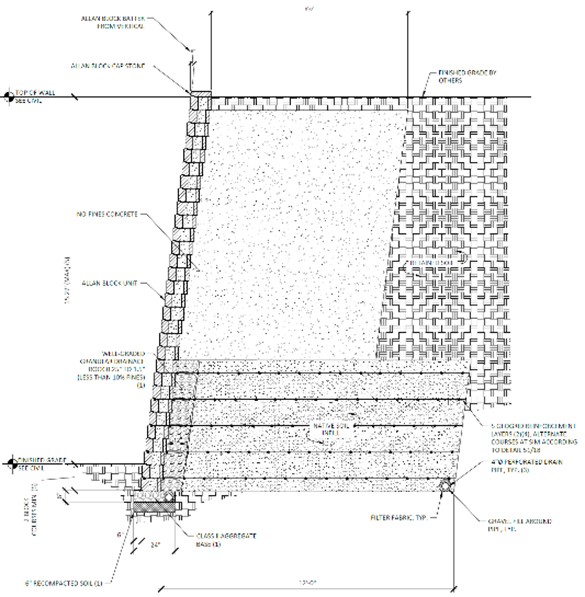
Design:
Smith Structural group reached out to Allan Block’s engineering team for assistance on this complex project. The experienced team at Allan Block was able to walk them through the design process of using NFC in Allan Block’s Design Software, AB Walls 3D+Terraces. Working with Allan Block, Smith Structural Group was able to create a complex composite structure design for the site, where they decided to use geogrid reinforcement for the bottom 8 ft (2.4 m) of the wall and NFC for the top half. By using NFC on the top of the wall, they no longer need to worry about future utility maintenance in the roads’ right of way.
The bus pad for the adjacent road required enough space for wheelchairs and other mobility vehicles to access the bus, per ADA guidelines. They created a bump out in the wall to make the required space for the ADA pedestrian ramp. The estimated cost of the completed Allan Block retaining wall designs came out to be much less than the cast-in-place wall. The cast-in-place wall footing alone was about the same price as the whole Allan Block wall. Without the use of NFC and the support from Allan Block’s engineering team, the developers would have been limited to a cast-in-place wall, essentially doubling their expenses
Build:
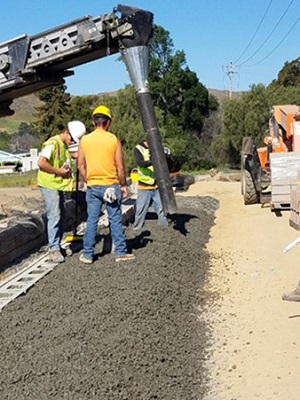
After creating the plans, the wall was successfully installed by Homeland Engineering. The installation process was fast-tracked and had reduced costs due to the use of NFC on the top half of the wall. Building walls with NFC was similar to building with structural fill, the first step was to lay out the first course of block on top of the geogrid reinforced section of wall. Next, Homeland Engineering filled all the voids in the first course and backfilled up to the specified depth with NFC. They poured the NFC in 2 course vertical lifts to allow for the installer to easily rod the NFC into the cores of the lower courses ensuring the voids were full. It was not required to let the NFC cure between pours because it starts to cure soon after being placed.
NFC backfill saved Homeland Engineering a considerable amount of time because they did not have to compact the entire infill zone in 8 in (200 mm) lifts. NFC does not require compaction or compaction testing because it’s intended to be a permeable concrete with voids, allowing for superior drainage. NFC eliminates the need for wall rock in the cores and behind the wall facing, furthermore reducing the number of materials and steps required. Additionally, by using NFC with Allan Block retaining wall units, contractors can effectively eliminate the need for heavy equipment on site. This means retaining walls can be installed with smaller crews, smaller equipment, and further reduced costs.
Bob LaVigne, an Allan Block Certified Contractor and Master Wall Builder of Homeland Engineering, contributed the success of this project to the clear communication between all parties involved. Allan Block’s engineering team worked with the developers, engineers, and installers to find solutions to this tricky site. Bob mentioned that from the developer’s position, “the easiest path of least resistance was to just put a cast-in-place wall on the site but then again they would have spent a lot of money doing that”. With quality products and substantial engineering support provided to this project, Bob stated that Allan Block had “proved itself, as Allan Block does time and time again, to be the solution for the conventional and unconventional options that are out there.”
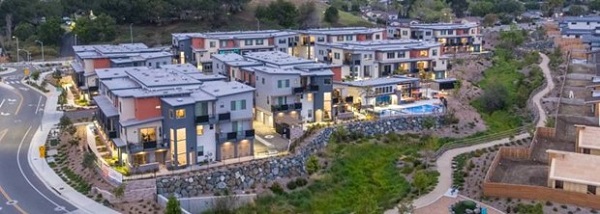