Project Information
Name: Weston Corners
Cary, NC
Product: AB Ashlar Blend Pattern
Size: 10,000 ft2 (930 m2)
Wall Builder: Delta Development, Raleigh, NC
Project Foreman:Clemente Project Mgr: Bill
Allan Block Manufacturer:
Fay Block - Fayetteville, NC
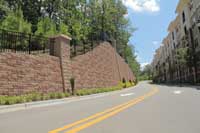
Large barrier wall that steps up to top with pillasters for design affect
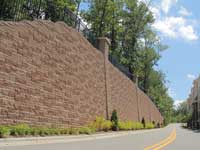
Other Reinforcement Options Save the Day
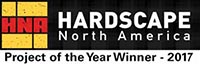
Weston Corners is a brand new luxury mixed-use development in Cary, NC. The site required several significant retaining walls during construction, one in particular and in close proximity to the property line, street and a building. This retaining wall was originally designed as a Cast in Place (CIP) wall with brick pilasters, but the bids for construction of such a project came back drastically over budget and at that time, the owner went to Delta Development for a solution.
Gib Lyttle (the owner of Delta Development and Allan Block Master Wall Builder) immediately began thinking of an Allan Block retaining wall with a special pilaster block (an AB block that has a 2 in. (50 mm) thicker face than a traditional unit) which he had seen used on a project in Oregon. Lyttle reached out to Fay Block Materials, the local Allan Block producer and they began researching and reviewing possible solutions.
Working with TerraTech Engineers, the group came up with the idea of a 25-30 ft (7–9 m) tall Allan Block Collection Ashlar Blend patterned retaining wall with a unique deeper faced unit to create the appearance of pilasters or columns. Lyttle thought this solution would provide the owner with the aesthetic they were looking for at a cost they could handle. The groups involved, TerraTech Engineers, Delta Development and Fay Block presented their option to the owner for review and their proposal was accepted.
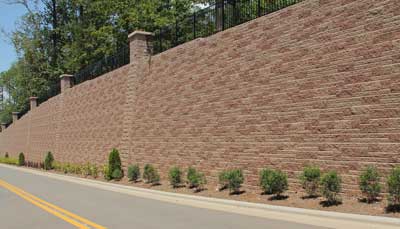
Immediately following approval, the design of the segmental retaining wall by TerraTech was completed. There were several demands with the site and the design of the retaining wall was challenging, but their thorough review and planning resulted in a wonderful project. One of their first challenges included a gas easement near the back of the wall which eliminated the ability to install the wall in a typical manner with geogrid soil reinforcement. The solution was to create a shotcrete wall with soil nails to reinforce the soil mass and avoid cutting into the gas easement. In addition, this was a cut site and the “cut” would include excavating to an elevation approximately 30 ft (9 m) below what was then,existing grade. The biggest challenge with completing the cut was that the entire depth of cut would be through bedrock material which meant blasting their way to the elevation needed.
When they finally reached the bottom elevation, groundwater became a problem and constantly filled the bottom of the cut. They had to come up with a primary drainage plan to be placed in between the shotcrete and soil nail structure and the Allan Block wall which included weep holes in the shotcrete which tied into a pvc pipe that was encased with concrete and ran behind the wall eventually tying into the storm system to reduce the likelihood of water issues. The block was installed in approximately six weeks, but the blasting, water management plan along with the shotcrete and soil nail portion took much more time.