Project Information
Name:
The Woodlands
Cottage Grove, MN
Product: AB Classic
Size: Wall 1 - 800 ft2
(250 m2)
Wall Builder:
Hardscapes Construction
Burnsville, MN
Allan Block Manufacturer:
Amcon Concrete Products, St. Cloud, MN
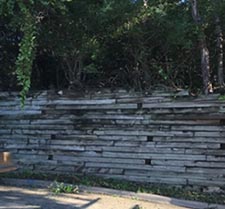
Before
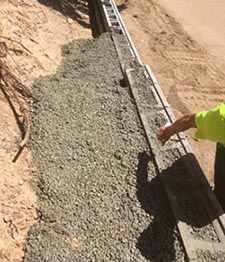
Allan Block and No-Fines Offer Cost Savings
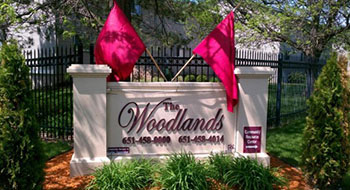
Woodlands Park Apartments is an affordable community located in Cottage Grove, MN. This community consists of six buildings with 180 individual units. Woodland Park had multiple timber retaining walls that were rotting away, looked unsightly and were becoming a major concern for the owner. One wall in particular was in need of immediate replacement due to its structural integrity and close proximity to the driveway.
Plan:
Amcon Concrete Products along with a representative from Allan Block, worked with the Project Manager to review feasibility of designs, walk the site and assist with determining possible solutions for the project. There were several solutions that were explored with the initial thought to use a Big Block design. After their initial conversation, other possible design options were explored such as using the Allan Block SRW system with no-fines concrete. Both designs could accomplish the task at hand, which was if the existing timber wall would be left in place and refaced or removed entirely. With the multiple design options available, Amcon offered design comparisons and in coordination with the wall installer, Hardscapes Construction, were able to provide price comparisons for both the Big Block and Allan Block with no-fines concrete. With all of this coordination and discussion taking place before the project was out to bid, the specifications came out with Allan Block with no-fines concrete and Big Block as options.
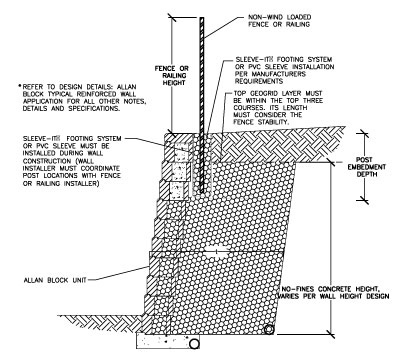
Project Design Detail
Design:
Big Block and Allan Block with no-fines concrete designs utilize the same calculations. Big Blocks are designed as a gravity wall system that relies on the weight of the face units to resist the loading, Allan Block using no-fines concrete is analyzed the same way. By using no-fines concrete as the infill material the concrete and the Allan Block units create a cohesive mass, essentially creating a big block on site. Creating the mass on site offers potential cost savings because of the manufacturing efficiencies of Allan Block, reduced freight cost and installation ease as well.
Build:
Hardscapes Construction of Burnsville, MN, an Allan Block Certified Contractor was awarded the project using the Allan Block and no-fines concrete solution with the deciding factor as the cost savings. According to Dave Klein, project manager with Hardscapes Construction, the cost savings was around $12,000-$13,000 on just the first wall of roughly 800 ft2 (250 m2), which was significant. As the project continues the savings will most likely become more drastic – a benefit many owners have experienced when comparing the two systems.
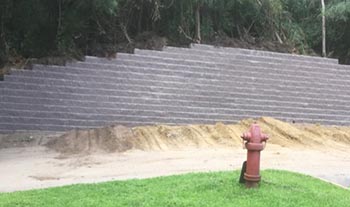
“There are applications where no-fines concrete is perfect, and this is one of them” Dave Klein – Hardscapes Construction. One of several aspects that made this an ideal application was the fact that it was a timber replacement wall with limited excavation capabilities. This established development had a driveway below and wooded area above with little room to install a traditional segmental retaining wall using geogrid. By using no-fines concrete the infill area was a fraction (up to a 50% reduction) of what would be needed for a typical geogrid application. This leads to less excavation which accommodates the site constraints above the wall, such as existing trees.