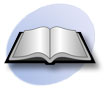
Print Case Study
Project Information
Name: Braemar Ridge Plaza
Bloomington, Minnesota
Product: AB Fieldstone,
Sierra Series
Size: 4200 ft² (390 m²)
Local Engineer: Ron Vickery, Vickery Engineering and Consulting, LLC
Wall Builder: David Harris, Harris Construction
Allan Block Manufacturer:
Amcon Block and Precast, Inc. - Saint Cloud, MN
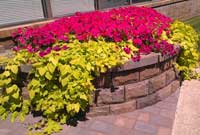
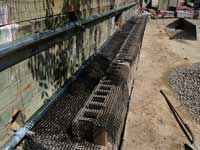
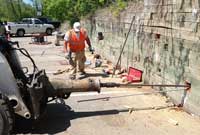
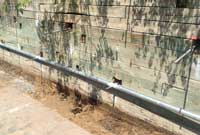
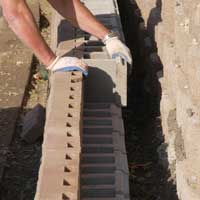
Braemar Ridge Office Plaza was starting to show its age. The new owners were looking to add new life into the building and the site to attract new clients as well as hold on to the ones they already had. The exterior rehab was straight forward. The building was cleaned and refaced with aluminum fascia, windows, and new sidewalks. But the site work was more complicated. The building was first built in the mid-seventies on a somewhat hilly site which required retaining walls. In the seventies, wood timber walls were very popular and the Braemar Ridge site still had a few to be replaced. The site also had other walls that over the years were replaced with a variety of different segmental retaining walls. The current site was a mess of varied wall conditions and looks.
Plan
The owners sought out the assistance of Allan Block Corporation, who they have worked with on other properties as well as their local manufacturer, Amcon Block and Precast of St Cloud, MN to find a solution for the site. Together with the design assistance of Ron Vickery of Vickery Engineering, the site review and planning started. The owners reviewed all of the block choices and quickly decided on Allan Block Fieldstone for its incredible aesthetics and versatility.
The site had a number of smaller walls, as well as one larger wall to replace. The AB Fieldstone with its optional short or long anchoring units would easily work for any of their conditions. Vickery Engineering utilized this versatility in their designs because the list of wall design requirements was long. The site currently had multiple wall types to consider updating or replacing from simple gravity walls, typical geogrid reinforced walls, existing timber walls, and an old segmental retaining wall so as to maintain the common look throughout the site.
Design
VickeryEngineering started work by laying out all the walls and deciding which walls would have what type of reinforcement. They used AB Walls 10 Design Software to design all of the walls needing reinforcement. With the multiple types of walls the design was going to incorporate geogrid, soil nails as well no-fines concrete.
Vickery did hand calculations for the walls requiring soil nails through the face of the wood timber walls. The soil nail walls design required three things; the spacing of the nails, and the diameter and length of the spreader bar. Once the nail spacing is determined, the horizontal force on the spreader bar can be determined based on active earth pressure and surcharge forces on the wall facing. Because the wood wall was in sound condition the number of nails were based more on the pipe size than the need for support. Vickery designed the wall to have about 24 in. (600 mm) of working space between the wood wall and the back of the block. This allowed space for the installer to work with the grid and spreader bars with room for placing and compacting wall rock. There are a few ways to connect the facing to the spreader bar, but Vickery chose the most common way by placing grid between the lower courses and bringing it up around the back of the pipe and back to the wall between the next two courses above.
The large 20 ft. (6.1 m) SRW wall that the owners wanted to update was the next challenge. Because the wall was a segmental wall, the individual units could have been unstacked; leaving the geogrid layers in place and then restacked using the new AB Fieldstone units by reconnecting the grid as the wall is reconstructed. This is a complicated process for the installers and takes great care to not damage the in-place geogrid during dismantling of the old wall. Vickery and the owners decided to sacrifice the old wall by leaving it in place and building the new AB Fieldstone wall in front of it. There are a few ways of doing this but space in front of the wall was not overabundant. It was suggested to build the new walls with about 6 in. (150 mm) of clearance between the face of the old wall and the back of the AB Fieldstone unit then filling the cores and void with no-fines concrete. The no-fines would adhered to the split-face of the old wall and solidified into the voids of the AB Fieldstone short anchoring units, making a continuous solid connection between the new and old walls.
Build
Harris Construction was contracted to build the walls because of their experience in building various types of reinforced walls. The soil nails they chose was a Manta Ray driven anchor system which was easily placed through holes they cut in the wood wall face. The nails were driven with a hydraulic ram. Once the nails were installed they attached the spreader bars to the nails and coupled them together in continuous rows.
After preparing the base and setting the first course, the installation proceeded similar to any other geogrid wall application. Harris made sure to use clean wall rock to facilitate easy compaction and ultimate drainage between the old and new walls
When facing the old SRW wall with AB Fieldstone and no-fines concrete, Harris and his crew were off to the races since they could stack the units and place the No-Fines as fast as they could. The placement of No-Fines concrete requires only minimal rodding to consolidate and can be poured in 2-course lifts. The set time is very short which allows work to continue at a high pace. The two-piece AB Fieldstone units are so the workers could place more square footage per day.
In the end, this very complicated site was tamed by the versatility of the AB Fieldstone Wall System. When all of the walls were completed the owners of Braemar Ridge were happy with the consistent look throughout the site, the ease of installation with multiple reinforcement conditions, and for all of the cooperation between all the parties.