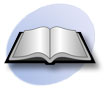
Print Case Study
Project Information
Name: Evergreen Community Association
Woodbury, Minnesota
Product: AB Fence with Ashlar Pattern
Size: 1400 ft (427 m) long 8 ft (2.4 m) tall
Allan Block Manufacturer:
Amcon Block - Saint Cloud, Minnesota
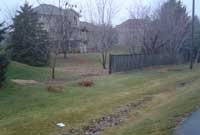
ECA Project - Before: The existing cedar fence had deteriorated beyond repair and needed to be replaced
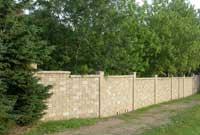
ECA Project -After: a fence option that was maintenance free and enhanced the curb appeal of their main entrance
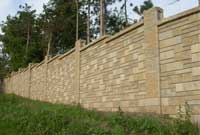
Considering both the average installation costs, expected life cycle of the product with any future maintenance costs, the AB Fence provided the best value
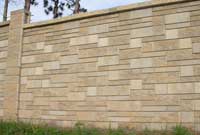
By choosing a concrete fence the amount of sound that traveled through the barrier, sound transmission, is greatly reduced
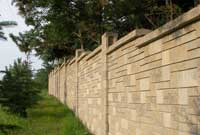
The fence needed to deal with a 40 ft (12.2 m) grade change, the panels had to step down at both the post locations and, within the panel itself.
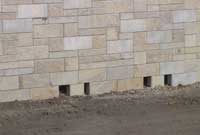
There were specific drainage points that were required to ensure that backyards would not flood. The bottom bond beams were constructed with openings to allow any water to flow through the fence.
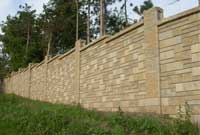
To carry the AB Ashlar Pattern look throughout the full panel, a single course pattern was used to build the bond beams.
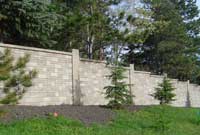
By using the AB Fence the sound was reduced by twice as much when compared to a wooden or vinyl product
Evergreen Community Association Concrete Fence Project
It was a classic case, an existing residential development starting to feel or actually hear the problems of a growing community. The Evergreen Community Association (ECA) in Woodbury, MN, an eastern suburb of Minneapolis and St. Paul, was sculpted on the site of a former Christmas tree farm back in 1980, and since that time, the population has quadrupled in the City of Woodbury. In 1985 the ECA constructed a 6 ft (1.8 m) cedar fence on the eastern edge to add a little privacy to the homes as the traffic increased along the bordering roadway. Now, 23 years later, the ECA was facing two major problems, deterioration of the existing fence and increase traffic noise. After researching their options the AB Fence System from Allan Block was the solution.
PLAN
The existing cedar fence had deteriorated beyond repair and needed to be replaced. It was becoming an eyesore and the main entrance to the association was framed on either side by this fence. Simply replacing the fence with a second cedar fence was considered, but the future maintenance of a wood fence was not heavily favored. The association was looking for a fence option that was maintenance free and enhanced the curb appeal of their main entrance.
Through their investigation, the AB Fence proved to be the best option. The fact that the system was built using mortarless, stackable concrete blocks meant the system would have not only the proven performance of reinforced concrete and long term durability, but also a reduction in total cost when compared to other concrete fencing options.
The first task was to create a cost comparison between different 8 ft (2.4 m) fencing options. By comparing these alternatives and considering both the average installation costs, expected life cycle of the product with any future maintenance costs, the AB Fence provided the best value. To make the choice even easier the association found that by combining the four different AB Fence panel block shapes, an Ashlar Blend pattern was created to best fit the look and feel of the surrounding area.
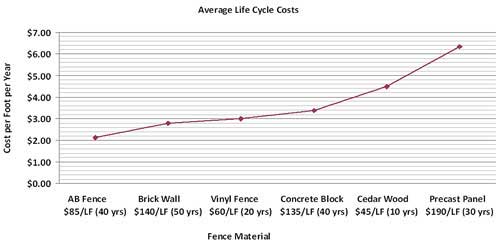
Fence Product Comparison Chart
The second issue was the traffic noise coming from the four lane road that ran along the eastern border of the development. By choosing a concrete fence the amount of sound that traveled through the barrier, sound transmission, is greatly reduced. The chart compares the transmission loss in decibels (dB) of different fencing materials. By using the AB Fence the sound was reduced by twice as much when compared to a wooden or vinyl product. The AB Fence system provided all the benefits of a long-term, cost efficient solution and sound abatement they were looking for.
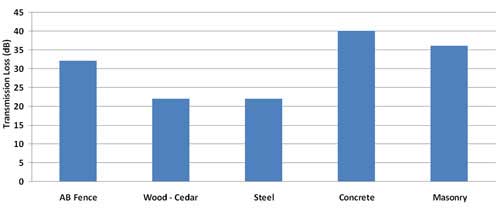
Fence Sound Transmission Chart
The ECA understood that all 408 homes within the association were not going to receive the same benefits from the AB Fence. The homes that bordered the eastern edge would receive the maximum benefit from the sound reduction and the property enhancement by replacing the cedar fence with the beautiful Ashlar Blend AB Fence. Therefore, the ECA proposed that these homeowners pay 50% of the cost while the ECA would pay for the remaining 50%.
In order for the ECA to finance their 50% portion of the fence they worked with a local bank to obtain a loan that would cover the initial fence costs. To pay for the loan each of the 408 homes would only need to pay $125.
The ECA needed to propose a fence assessment to the association, which outlined the following two payment plans for the association’s residences, (1) a $30 per year payment for the next five years or (2) an upfront payment of $125. According to the ECA’s bylaws, in order for this assessment to pass it needed an approval vote from the majority of the residences. This was sent out to the homeowners for a vote and passed easily.
DESIGN
The fence was to be located in the same place as the existing wooden fence; however, this required a little creativity in design and layout. The fence height was expanded to 8 ft (2.4 m) to further reduce noise transmission. The fence needed to accommodate over a 40 ft (12.2 m) grade change, which meant the panels had to step down at both the post locations and, at times, within the panel itself.
Allan Block Corporation worked with the ECA to come up with the preliminary design for the Ashlar Blend AB Fence. The fence was designed with a wind loading of 80 mph (129 Km/hr) with moderate exposure. This design allowed the 8 ft (2.4 m) tall fence to have spacing between the posts of over 16 feet (4.9 m). The designed pile footings for the fence were 2 ft (0.6 m) in diameter and 4.5 ft (1.4 m) deep, however the City required a 5 ft (1.5 m) minimum depth. The panels were designed with reinforced bond beams located at the top and bottom of the panel sections. The bond beams were constructed by using a #4 reinforcing steel between two courses of block that were grouted together. Since the panel sections were 12 courses tall, this meant that eight courses for a total height of 5.3 ft (1.6 m) were dry stacked between the bond beams making the AB Ashlar Pattern easier to install. To carry the AB Ashlar Pattern look throughout the full panel, a single course pattern was used to build the bond beams. The design also called for flipping random blocks around to change the appearance of the fence. This ensured that both sides of the fence had the aesthetics of a random AB Ashlar Blend.
Additionally, water management was crucial. There were specific drainage points that the City of Woodbury required to be maintained to ensure that backyards would not flood. Working with the City to identify these areas, the contractor, Sierra Exteriors, was able to construct the bottom bond beam with openings to allow any water to flow through the fence.
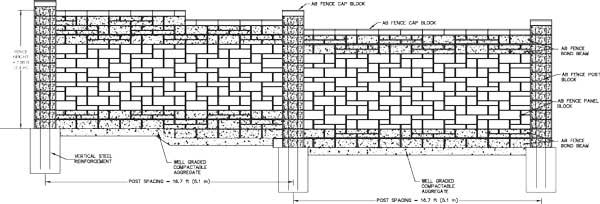
Allan Block Fence Panel Design
BUILD
Construction began in November which allowed the contractor to keep his crews busy during the winter months. Like any successful fence project the contractor started with marking out the proper locations for the pile footings. Following the AB Fence Installation Guide and using the jigs made the job easier. As the pile footings were being excavated, they encountered boulders and rocks below grade. Each rock had to be removed to maintain the proper location of the post. The pile footings were then filled with concrete and the jigs were used to ensure that the vertical steel was properly positioned.
Once the footings were completed, the posts and panels of the AB Fence were started. The fence design used the full sized AB Fence Panel Block for the base. This made it easier to install the panels straight and level and simplified the installation of the reinforcing steel and 9 gauge wire stirrups through the bond beam. To finish the bond beam the cores of the panel blocks were filled with concrete. Because of the winter conditions, the contractor did have to protect the fresh concrete when the temperature dropped below freezing during the evenings. Temporary tents, heaters and insulated blankets were used throughout the project.
With the high visibility of the project, everybody was interested in the color of the block and the pattern options for the fence. The local Allan Block manufacturer, Amcon Block, provided a beautiful three colored blend unit for the project. To add to the random pattern look of the Ashlar Blend, random blocks were flipped backwards to create a change in the face appearance. This meant that both the City of Woodbury and the homeowners enjoyed the beautiful aesthetic color and finish of the AB Fence System. A local building inspector from the City of Woodbury commented that, “This fence has just set the standard for the fence projects in the City and it has exceeded our expectations”.